APPLICATIONS
Thermal links provide overheat protection for electrical products such as home appliances, battery packs, motors, power supplies, transformers, heating and air-conditioning equipment and various electronic devices.
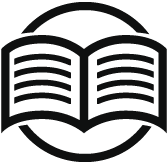
Our Resource library includes product specification sheets, catalogs, technical product information, links to manufacturer’s web sites and manufacturer’s installation cautions for the Elcut and SEFUSE® thermal links and battery protectors.